In the rapidly evolving world of cultivated meat production, the integration of digital twins and simulation technologies is revolutionizing the industry. These advanced tools are not only optimizing the production process but are also significantly reducing the costs associated with building and operating cultivated meat factories. Let’s delve into the transformative impact of these technologies we use in FUDZS.
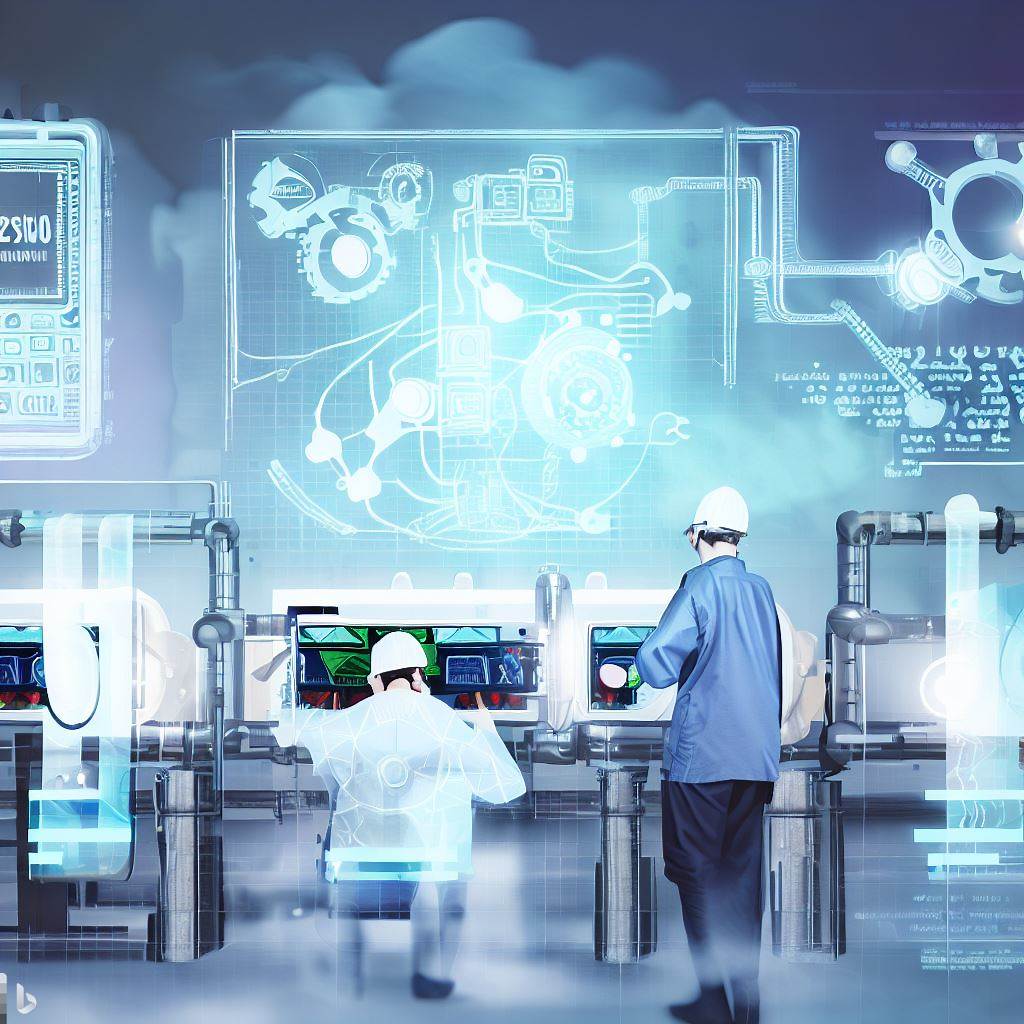
The primary goal of cultivated meat producers is to offer a sustainable and ethical alternative to traditional meat at competitive prices. Digital twins, which are virtual replicas of physical systems, play a pivotal role in achieving this. By simulating the entire production process, these digital models allow producers to identify inefficiencies, predict potential issues, and test various scenarios without the risks associated with real-world experimentation. In FUDZS, we are working at several levels. First, we simulate our future bioreactor to understand precisely the impact of a little variation in inputs on meat output flow. It’s a complex process because we can act on many input parameters, from the geometry of the bioreactor to the composition and physical conditions of entering fluids. At a bigger level, we also simulate the complete production process to identify weaknesses as soon as possible, like immobilization times of product or dependencies of certain devices. As a result, the production process can be fine-tuned to maximize yield and minimize waste, leading to a significant reduction in the final price of the meat.
Building a cultivated meat factory is a massive investment. However, with the aid of the digital twin of our devices, the costs will be substantially reduced. Before any physical construction begins, a complete digital replica of the factory will be created. This virtual model will be used to test different layouts, equipment placements, and workflows. By identifying the most efficient design through simulation, investors will ensure that every dollar or euro spent on construction yields the highest possible return on investment! Of course, this digital twin of the factory will be updated in real time to simplify the maintenance. Traditional maintenance schedules are often reactive or time-based, leading to either unplanned downtime or unnecessary servicing. Our Digital twin will change this by continuously monitoring the real-time data from factory equipment and comparing it with the virtual model. This will enable the identification of any discrepancies or early signs of wear and tear. By predicting when a machine is likely to fail or require servicing, maintenance will be scheduled proactively, reducing downtime and extending the lifespan of the equipment. This not only saves on maintenance costs but also ensures that the production line runs smoothly, contributing to the overall efficiency and profitability of the cultivated meat factory.

The complexity of operating a cultivated meat factory requires a highly trained workforce. Traditional training methods can be time-consuming and expensive. Enter virtual reality (VR) simulations based on our digital twins. These immersive training environments replicate the exact conditions of the factory, allowing operators to learn and practice their tasks in a risk-free setting. This not only speeds up the training process but also ensures that operators are well-prepared to handle real-world challenges. It is a very important part of our deployment strategy because, it will allow us to train people before the building of the factory.
The integration of digital twins and simulation in bioproduction is just the beginning and, at FUDZS, we want to be true pioneers. It’s why we are establishing partnership with major worlds actors of the field. We are also incorporating artificial intelligence (mostly machine learning algorithms at this time) in our simulation to increase our capacity to find the better production scenario for a given situation. We are also exploring the amazing world of blockchain technologies to create a more trustful way of communication with the final customer. But it’s another story!
The future of cultivated meat production is digital, and the possibilities are limitless.
Interesting external sources :
- Applications of process and digital twin models for production simulation and scheduling in the manufacturing of food ingredients and products
- Digital Food Twins Combining Data Science and Food Science: System Model, Applications, and Challenges
- Industry 4.0: How Digital Twins in Manufacturing are Changing Industrial Production
- 15 Digital Twin Applications/ Use Cases by Industry in 2023